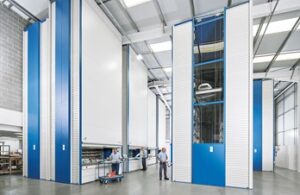
In the years ahead, intralogistics will be transformed dramatically – in ways much like those seen in manufacturing processes. Lean-Lift is the answer.
Modern production processes in an ever-changing business environment require the deployment of trendsetting technologies in all kinds of industries. Innovation and creativity are both decisive factors when it comes to smart production solutions such as high-mix/low- volume manufacturing.
In recent years developments in robotics and automation solutions have experienced a massive surge as more and more industries adopt efficient applications.
A fully automated put and pick processes for the Lean-Lift® systems with support from a mobile robot has been developed.
An optimal automated warehouse storage system equipped with a touchscreen was developed for trade fairs which enables users to retrieve a can of chips from storage. The robot – which is comprised of a driverless transport system and an articulated arm – performs the pick operation launched from the touchscreen. The robot autonomously removes the can from the multifunction container and then brings the can directly to the user.
The orchestrated interaction between lift system and robot unleashes huge potential for diverse industry applications.
Similar systems are already being used to automatically pick and transport injection molds, fixtures, tools and adapters for electrical device tests to and from production lines. For example, the robot can bring packages that have been opened on the production line back to the storage system and put them back into inventory.
The Lean-Lift ® can also be used for fully automated buffer storage of items between various steps in manufacturing processes.
Humans and Robots Working Together
The mobile robot system performs tasks autonomously and moves from one workplace or production area to the next on its own.
In the future humans and robots will be working together in teams. The robots are equipped with integrated laser scanners, enabling them to move autonomously, safely, and precisely among their human counterparts at work.
They can also do heavy work or monotonous tasks. There is also an additional advantage of this new technology: Humans and robots will be able to stand side by side and pick items from the same automated storage system.
Innovative intralogistics solutions – combined with intelligent software – can sustainably optimize efficiency, quality, and cost-effectiveness.
Another innovative solution is the EcoDrive CO2 reductions they have made possible. Thanks to efficient energy recovery, maximum security of the storage articles, no limitation to the height of the storage goods, and optimal ergonomics is a wonderful storage solution!
Depending on the traversing rate, up to 40 % of the energy fed in previously for the upward run can be returned to the supply network!
The EcoDrive helps to save energy and consequently to reduce costs. A new kind of frequency converter uses the energy of the descending extractor and converts it back into electrical energy. This is then fed back into the supply system and can be used elsewhere, for example on other Lean-Lifts ® in a network.
Usually the articles in a pick list are located on different storage containers. With Pre-Store Buffering® , the time needed to access consecutive containers is considerably reduced. While the operator takes the required articles from container q in the access point, the extractor is already bringing container w to a storage location directly behind the access point (this location can be pre-defined as required). Pre-Store-Buffering® Time saved by automatic buffering has perfected this system and developed the Lean-Lift ® in DualDrive® design.
The Lean-Lift ® with DualDrive® design boosts order picking performance substantially. Pick lists with articles stored on different containers can be processed at a considerably higher speed. This saves time and therefore costs!
DualDrive® doubles the performance The EcoDrive helps to save energy and consequently to reduce costs. A new kind of frequency converter uses the energy of the descending extractor and converts it back into electrical energy. This is then fed back into the supply system and can be used elsewhere.
If you would like more information on this innovative solution, contact us today.